Fondée en 1992 avec un capital social de 5,2 millions de dollars américains par des entreprises australiennes à propriétaire unique, et possède une zone d'usine de 72 000 mètres carrés.
Bouchon Moule
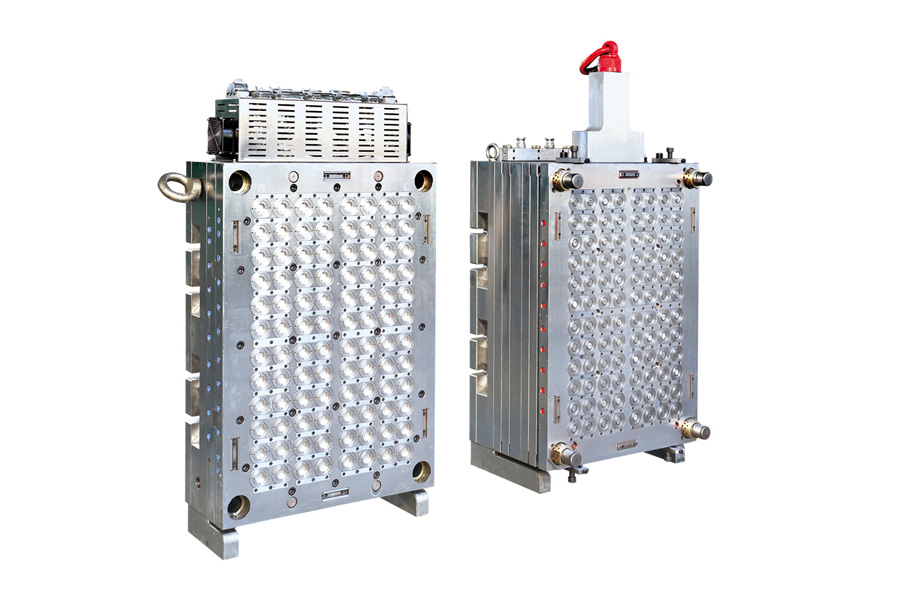
Le composé de moule 210 est lié à la matrice 206 et à la grille de connexion 205. Le capuchon 220 est fixé à la matrice 206 par un adhésif 217, et le capuchon est fixé à la matrice avec un deuxième adhésif 216. Le moule 300 est un dispositif utilisé dans le processus de moulage. Il fonctionne conjointement avec le substrat 200 pour produire un réseau de boîtiers. Il comporte deux sections : une section de moule supérieure 302 et une section de moule inférieure 304. La première est conçue comme une barre de cavité amovible, tandis que la seconde sert de moule rigide. La section de moule supérieure 302 comprend une pluralité d'extensions 230 qui s'étendent de les coins du corps du moule. Les extensions ne s'étendent de préférence pas au-delà des bords du substrat. Lors de la création d'un moule de capuchon personnalisé, il existe plusieurs options pour créer le bon aspect. Une option consiste à utiliser une série de moules rapides. Ces moules sont conçus pour s'adapter à la tête individuelle d'un client sans aucun tracas ni conjecture.
Les moules rapides ont été testés et éprouvés pendant des années. Une autre option consiste à utiliser les bonnets de Superhairpieces. Ces moules sont disponibles en 18 tailles et ensembles de contours différents, vous pouvez donc choisir celui qui convient à chaque client. Les capuchons sont étiquetés avec les mesures correctes, ce qui facilite leur mise en place sur la tête d'un client. Le masque de soudure 116 protège les traces conductrices des puces semi-conductrices. Cette housse de protection est formée par les procédés de moulage par transfert ou moulage par injection. De plus, ils ont des coins chanfreinés qui exposent les coins du substrat. Lorsque le substrat est manipulé, le masque de soudure à ces coins est susceptible de se fissurer, en particulier pour les boîtiers de grande taille. Le masque de soudure est une fine couche de polymère généralement de couleur verte. Il protège le cuivre en dessous de l'exposition à l'environnement et empêche l'oxydation. Il empêche également les moustaches métalliques de se développer sur le PCB, ce qui peut provoquer des courts-circuits.
Lorsqu'il est correctement conçu, un masque de soudure peut empêcher l'oxydation du cuivre et également prolonger la durée de conservation du composant. L'un des facteurs clés de la production de moulage de capuchons est le temps de refroidissement. Il peut représenter plus de 80 % du temps de cycle total. Le temps nécessaire pour refroidir un bouchon varie selon le matériau, le type de cycle et la forme de la pièce. La figure 1 présente une équation qui peut être utilisée pour estimer le temps de refroidissement. L'épaisseur de paroi et le matériau sélectionné pour le moule jouent un rôle important dans la détermination du temps de refroidissement. L'ingénieur concepteur de moules doit s'assurer que les canaux de refroidissement sont placés dans les meilleures positions possibles pour maximiser l'efficacité du refroidissement. De plus, l'ingénieur de procédé doit s'assurer que les pièces sont remplies le plus rapidement possible. S'il n'y a pas assez d'énergie de refroidissement disponible pendant les phases de remplissage et d'emballage/maintien, les pièces peuvent geler.